The weld inspection system tracks every inch of tubing coming out of Tata Steel’s mills in Oosterhout, so when a problem arises, operators know where and when it happened.
Before Marcel Marijnissen joined Tata Steel’s Tubes Netherlands division, he led projects for a European lighting manufacturer. With that switch from glass to steel tubing, seeing errors in the final product isn’t quite as easy as it once was. Spot Welding Electronics
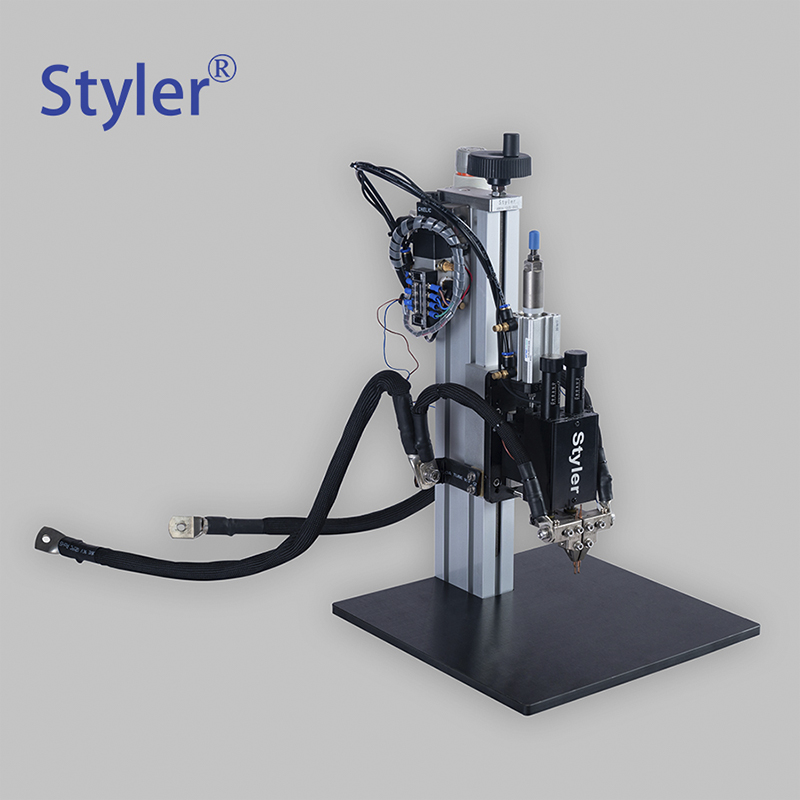
Perhaps that’s why the process improvement engineer can appreciate the results that Tata’s tube facility in Oosterhout, Netherlands, has gained from Xiris Automation’s WI-3000 Weld Inspection System.
About 300 people work at the Oosterhout plant, which makes round, square, and rectangular tubes for the automotive, furniture, heating and ventilation, and construction markets (among others). Tubes produced in Oosterhout are mainly made from carbon steel and range in width from 10 to 76 mm OD.
Precise and soft-spoken, Marijnissen has a special interest in providing the plant’s customers tubes that maintain tight tolerances—especially the ones used in automobile parts.
The laser-based Xiris inspection system can detect forming, welding, and scarfing defects down to 0.015 mm in the tubing flying off Oosterhout’s five mill lines in real time, providing Marijnissen and his teammates with data they never were able to get that quickly, if at all. The system has been designed to monitor such variables as bead height, deflection, scarf flatness, and undercuts.
Even veterans on the Oosterhout team have come to appreciate the system: Rather than trying to correct a problem they find in their product after running several lengths of sample tube and inspecting them, operators at Oosterhout now can track every inch of tube coming off the line in real time and adjust immediately.
“Even with experienced welders at the line, on the first trial, you have to wait for the operator at the end of the line—he takes a sample and says that the welding strength is OK, the forming is OK, or you have to readjust the forming,” Marijnissen said of the facility’s old process. “Then you have another 40 m of tubes produced, and then it’s overcorrected. So again, you have to produce 40 m. And then, finally, at the end of the line, the operator says that now the quality is good.
“That’s a lot of scrap.”
When Tata installed the system a few years ago on the first of its five tube mill lines, which mainly serves automotive customers, it was part of Marijnissen’s job to prove it out and also help train other team members how to use it.
How did it go? Well, the system is now operating on all five lines at Oosterhout. Tata installed its fifth system in 2021.
It didn’t take long for Xiris Automation’s WI-2200 laser-based welding inspection system to make believers of even the veterans at Tata Steel’s Tubes Netherlands division.
Marijnissen has to chuckle a bit when he talks about how the inspection system was received when it was introduced at the plant. Not because the system didn’t work—on the contrary, because it was effective enough to make true believers of every tube mill operator at the plant.
“Maybe the experienced welders were very critical in the beginning,” Marijnissen recalled. “They are very positive [now] because they see a change and they know, ‘OK, I know from my experience I have to change this setting or that,’ and they immediately see the impact. And for the new welders, they cannot do without it anymore. They do not know a life without the service.”
That’s been the reaction from more than one user of those inspection systems, according to Cornelius Sawatzky, sales manager for Xiris Automation in Burlington, Ont. The younger operators, fond of data, take to the system first. But sure to follow are the older operators, especially once they see how the system’s results serve as a repository of knowledge for everyone involved.
In that way, the system acts as a communication tool between different shifts on the tube mill line, but also between engineering and management, Sawatzky said.
“It’s an aid,” Sawatzky said. “It’s a tool [for] identifying the potential for a defect sooner … and ultimately reducing the probability of something being returned by their customer for nonconformance.”
Product falling out of tolerance for customers like automotive companies served by that first Oosterhout line can be especially costly, Sawatz