America’s reliance on overseas suppliers appears to be dwindling. Much of this is due to the stubbed toe we experienced during COVID-19 and the subsequent supply chain catastrophe, a situation further exacerbated by the ongoing trade war with China.
“From late 2020 all through 2021, the semiconductor industry was buying CNC machines at an unprecedented rate,” says Don Langley, western region sales manager for DN Solutions America Co., Pine Brook, N.J. (formerly Doosan Machine Tools). “These weren’t the traditional two-axis lathes and three-axis mills like you might expect—it was all advanced five-axis machining centers, multitasking lathes and pallet pool-equipped horizontals. Other industries are beginning to follow suit, and from what I see and hear, much of this is due to reshoring.” Manual Knee Milling Machine Factory
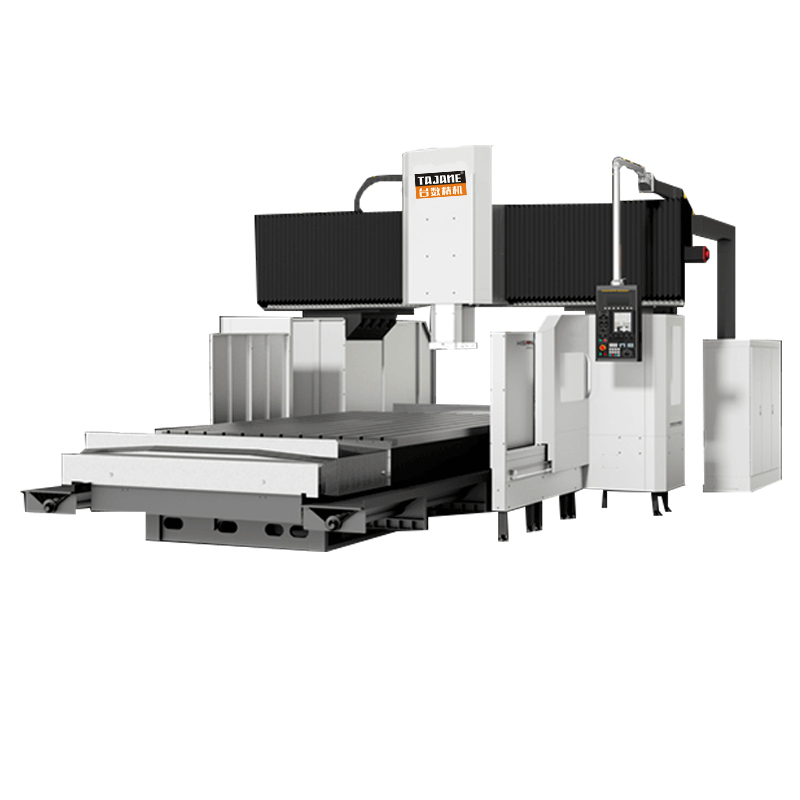
One of these industries is tool and die, the foundation for all forms of manufacturing. As with semiconductor, aerospace and medical, the materials here are typically tough and the tolerances are tight. These challenges help explain the push for more capable and inherently more complex machine tools.
Dave Ward, product marketing manager for Makino Inc., Mason, Ohio, noted this fact in Manufacturing Engineering’s Soup to Nuts of Dies and Molds from earlier this year, suggesting that five-axis machining centers are more productive and accurate than their three-axis counterparts, and are ideally suited for this type of machining work. “We visit a lot of shops, and there are three main trends right now: five-axis, five-axis and automation,” he said.
Unfortunately, it remains easier to build and buy machine tools than it is to find people to run them. Because of this, tool and die shop management is left in an awkward position—too much work and not enough workers—impeding growth. As with the domestic supply chain, however, efforts are being made to improve this situation.
There’s the aforementioned White House Jobs Plan, which allocates $100 billion to workforce development, but it’s no secret that public schools, community colleges and universities throughout the United States—together with numerous machine tool companies—have made significant investments in training the next generation of manufacturing workers.
Those who opt for careers in skilled trades will find manufacturing to be far different than what their parents experienced a few decades ago, and the tool and die industry is no exception. As Makino’s Ward and DN Solutions’ Langley point out, today’s world is increasingly one of automation and CNC machine tools that were only a fantasy when the bulk of veteran machinists were born.
“The labor problem is part of it, but some is being driven by limited floor space and the high cost of real estate, especially out here on the West Coast where I work,” says Langley. “Having machinery that helps complete parts in one or two operations means fewer setups and fixtures, less work-in-process, greater flexibility and a much smaller footprint.”
Tool and die shops are also asking for machinery that supports faster metal removal rates, adds Brock Herbert, senior applications engineer with Florence, Ky.-based Mazak Corp.’s North Central region. “Obviously, there are extreme accuracy requirements to consider in this environment,” he says. “But depending on the workpiece, there’s often the need for high-spindle speeds, with controls and servo systems able to process huge swaths of code very quickly.”
Again, much of this applies to aerospace and medical components, where complex sculpted surfaces and tough metals are commonplace. Tool and die raises this bar even higher with its extensive use of tool steels, often machined in the hardened state.
On the flip side, though, there are also the graphite electrodes needed to EDM mold cavities and other part features, a material that presents its own unique challenges and opportunities. This includes the material’s relative softness, its fragility and tendency to chip, and the need for robust dust control during electrode machining.
But all of these difficulties are quite manageable with the appropriate equipment and tooling, according to Alan Hallman, North American sales manager for MC Machinery Systems Inc., Elk Grove Village, Illinois (the importer and distributor of Roku-Roku, OPS Ingersoll, Mitsubishi Electric and other CNC machine tool brands). As such, he says, high-volume production of these ubiquitous tools is often the first piece of low-hanging fruit that shops pick.
“It’s not so much in tool and die, but certainly in the moldmaking area that shops are machining large numbers of electrodes,” Hallman continues. “And since there are end mills available that can cut graphite for maybe a hundred hours without appreciable wear, it’s a fairly straightforward exercise to automate these applications. This is why many shops begin their lights-out initiatives here.”
The first step in such initiatives is an investment in a high-quality machine tool—but perhaps not for the expected reasons. Yes, a rockin’ machining center is necessary for any shop looking to increase throughput, accuracy and part quality—whatever the industry segment or machining specialty—but it’s also a prerequisite to an often overlooked must-have for automation: process consistency.
To more easily achieve this, shops must be willing to embrace the Industrial Internet of Things (IIoT). Doing so means the ability to check in on machining processes from afar, but also opens the door to proactive machine maintenance, cutting-tool monitoring, toolpath and cutting parameter optimization, and other capabilities that tool and die makers can use to reduce costs and, most importantly, make sure the machine will still be making chips the next morning.
It’s a deep topic, and one that machine shops of all stripes must tackle to remain competitive. In the meantime, here’s what machine tool providers might recommend during a typical sales visit to a potential tool and die customer, although it’s important to note that no company offers a one-size-fits-all solution for such a broad segment of the manufacturing industry.
For example, Sean Shafer, segment manager for the die and mold market at Makino, might suggest either the company’s V100S or the D2 vertical machining centers. The latter is a pallet-changing, seven-axis machine with more than two meters of X- and Y-axis travel and a tilting/rotating HSK-A100 spindle that “assures the tool tip can be positioned to provide optimum contact” and reduce hand polishing of mold surfaces.
The five-axis V100S is also aimed at mold and die manufacturers, with a 20,000 rpm HSK-A63 spindle and equally large axis travels. Both machines are equipped with Makino’s Super Geometric Intelligence (SGI.5) servo control to address advanced motion control requirements.
Although designed for large mold components, these machines would be a welcome addition in many tool and die shops. Would they be the ideal solution? Perhaps not. The answer depends on part size, accuracy requirements, material removal needs, production quantities, and a host of other variables we don’t have time to delve into here.
“Diecasting, plastic injection molding, stamping and forming, progressives—each has similarities, but is also unique in some ways,” Shafer says. “For instance, moldmakers generally want the tool to come off the machine with the best surface finish possible, while super smooth cavities can be a problem for diecasters. And progressive die makers will have accuracy requirements that are much more stringent than other toolmaking sectors, even though they all deal with tight tolerances.”
Exacting tolerance is one of the reasons automation is difficult in this environment. And it’s why humans will remain in the toolmaking sector. “When you’re machining parts to within a tenth or two, you need an experienced machinist around to keep an eye on things,” asserts MC Machinery’s Hallman. “Add to this the fact that most of the work here is very low quantity, and you can see why automating tool and die work is often a struggle.”
A struggle, but not impossible. Hallman points to the company’s MEGA SSS family of five-axis machining centers from Roku-Roku as one of his go-to machines for shops that spend their days “chasing tenths,” particularly those competing in the smaller part arena. With linear motors, HSK-equipped spindles with up to 60,000 rpm, and a 31i-B5 high-speed processor, Al Contour Control II and five-axis machining package from FANUC, these machines are reportedly accurate “down to the 1,000th of a millimeter.”
As noted, Hallman has other options on his line card, including OPS Ingersoll’s Eagle line of five-axis machining centers, as well as numerous automation offerings. “We’ve installed several hundred material handling systems, including those from EROWA, 3R, FANUC and Mitsubishi,” he notes. “The first two are especially popular with tool-and-die makers, largely due to their integrated workholding and gripping capabilities, although all are amazing systems.”
Likewise, Mazak has no shortage of product offerings. “On the larger end, there’s our FJV line, a bridge-style vertical machining center that comes in three-axis and five-face configurations up to 160-inches in the X-axis,” says Jared Leick, machining center product group manager. “These are very robust machines that are quite popular with tool-and-die shops, but there’s also the VARIAXIS family of five-axis verticals, our HCN and HCR horizontals. … It’s a very broad lineup of machine tools.”
From his perspective as an application engineer, Herbert is quick to point out Mazak’s SMOOTH technology and user-configurable SMC (SMOOTH Machining Configuration) settings are quite popular with tool-and-die makers, among others. Both provide excellent control over the machine’s motion control systems, he notes, including cornering accuracy, look ahead, axis acceleration and deceleration, and other variables that can dramatically affect part quality, tool life and productivity.
“The control also provides a graphical representation of what each setting does with respect to the relative advantages or sacrifices you might make when tweaking any of the values,” Herbert says. “There’s no need to machine a part to see the results. And once the operator has everything dialed in with the optimal settings for a given job, they can save it with the part program for next time. It’s a really great feature.”
DN Solutions has a similarly broad offering, with more than 400 models, according to Langley. “However, five-axis machines have exploded in popularity over the past few years,” he says. “Our DVF 5AX vertical machining centers have been a big hit with this and other markets. These range from the DVF 4000 with a 400-mm table to the DVF 8000T with an HSK spindle, 18,000 rpm, and just shy of 40 inches (1,016 mm) in the X-axis.”
Not surprisingly, machines with 40” x 20” (1,016 x 508 mm) table travels remain the most common, at least for DN Solutions. So are 12K and 15K steep taper spindles, although Langley notes that many shops prefer Big Plus and competing forms of dual-contact interfaces for their greater rigidity.
And as one might expect, machine shops of all kinds are increasingly requesting options such as pallet changers, through-the-spindle and high-pressure coolant, in-machine probing systems, and motion control features such as FANUC’s AICC II and Smooth Tolerance Control or similar advanced options from Siemens, Mitsubishi and other control builders. All either support automation, increase productivity or both.
“Shops have also come to realize the importance of a kinematically accurate machine tool, one with plenty of mass and thermal stability,” Langley asserts. “This has always been true to a certain extent, but is more necessary now than ever. Given the ongoing labor shortage, it’s not like it used to be, where a skilled machinist knew how to make even a commodity machine sing and dance. Those days are gone.
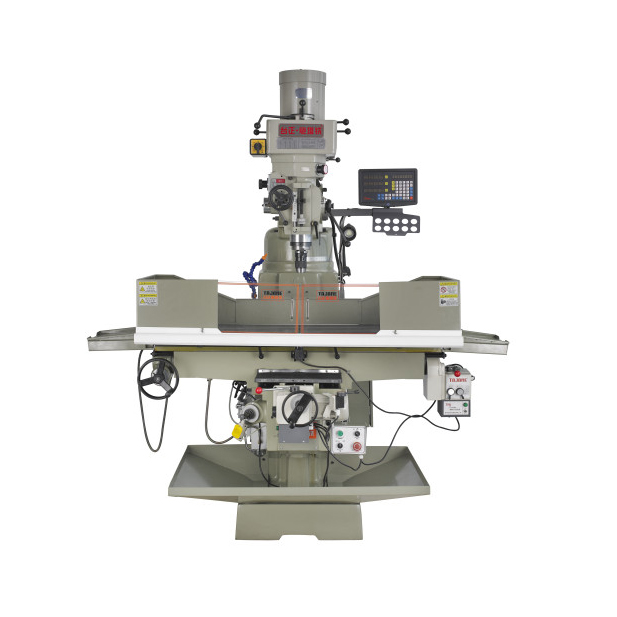
Large Vertical Machining Centers “Machine tools now must be highly predictable and accurate, no matter who’s running them,” Langley continues. “This fact is increasingly important with the tougher, harder materials and tighter tolerances like you see in tool and die, but also aerospace, medical, energy parts machining and so on. The industry is changing, and shops need to get on board with the newer technology or they’ll be left behind.