Understanding GeoGrids, GeoComposites, Geotextiles and Hybrid GeoMats
GeoGrids, GeoComposites (Grids and Paving Fabric Combination), Geotextiles (Paving Fabric and others) and Hybrid GeoMats (fabrics with a combination of fiber types) are all part of the ever-expanding line of Geosynthetics. These paving synthetics have different applications and provide different functions in paving applications. Each require different installation procedures for proper placement and to obtain the desired design benefit none install similarly. Geotextile Fabric Under Pavers
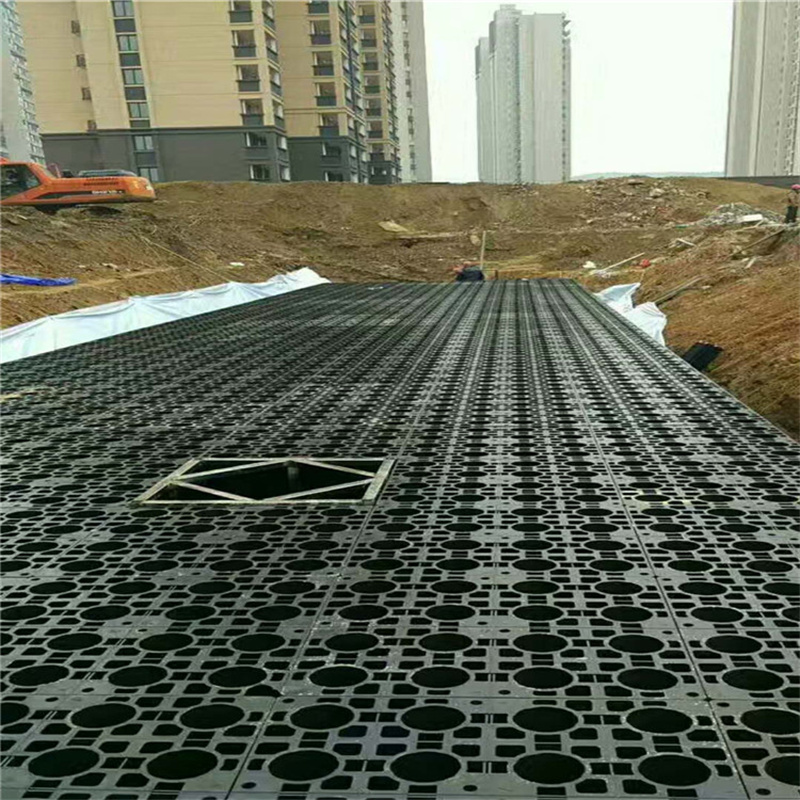
All of these may be beneficial in both small and large application for parking lots, driveways, streets, highways, airports and more. What is important is to determine what function or functions (benefits) that is trying to be obtained.
Any or all of these functions can be obtained with the proper selection of the Geosynthetic.
A. A moisture barrier interlayer membrane is for the control of surface water infiltration that breaks down the bearing capacity of the subgrade.
GeoGrids, which are manufactured from a variety of materials including fiberglass, polyethylene and polyester, are used for unstable base reinforcement. Metal grids were used in World War II to make rapid runways and roads. Paving GeoGrids are used for internal asphalt overlay reinforcement. They are very rigid, look like a fence and have openings (apertures) that can vary in size from small to large. They have very low or no elongation (stretch) and a high modulus that gives them high strength, maximum reinforcement and reflection crack prevention.
Paving GeoGrids come in various widths from 2 feet to 16 feet. The majority are manufactured from 5 to 13 feet wide. Width needs to be taken into consideration when installing. Smaller widths require more installation passes and usually more time to complete the installation. Smaller widths may install driving faster than slower with wider widths and have less wrinkles, depending on the manufacturer.
Paving GeoGrids must adhere to the pavement, so the paver does not lift them. They can adhere depending on the manufacturer differently.
A. A preinstalled adhesive that does not require a tack coat (oil)
B. With a light Geotextile fabric attached for adhering to a lite tack coat (oil)
C. Impregnated with a bitumen coating (oil similar to tack coat) that requires less or no tack coat
D. A GeoComposite with a thicker paving fabric that requires a tack
A Geogrid combined with a Geotextile Paving Fabric is called a GeoComposite. It provides both reinforcement, crack prevention and the interlayer membrane once the fabric is impregnated. It uses the same tack coat (oil) quantities for a paving fabric.
Installation by hand is easier than a fabric because of its rigid state but is very time consuming and labor intensive in the number of laborers necessary.
Machine placement is fastest. It requires some different installation techniques than fabric. Any tensioning needs to be to a minimum. If bars for alignment are used, they should roll and not glide over especially if coated with an adhesive or bitumen impregnated. The material does not stretch (elongate) and stretching system is detrimental. The grid must unwind freely with little or no impedance.
Placing grids on curves with grids will almost always require hand placement and the cutting of pie shaped wedges. The overlaps will be based on the manufacturer recommendation.
Each manufacturer has various grids, some with different thicknesses and each has different recommendations and requirements for application and tack coat (oil) and for placement of adjoining rolls for horizontal and longitudinal overlaps. There are no standard ASTM specifications for grids.
Some grids will overlap at joints and some grids will butt up. The same for dealing with cut wrinkles. Thinner grids may overlap while thicker grids may butt up. There may be a difference also when used within a chip seal.
Binders for grids can be hot tack coat (oils) or rapid set emulsions depending on their manufacturer recommendations. Oils will vary between .06 to .18 gallons per square yard without fabric. Emulsions require a 30% increase in application rate to account for evaporation and the extra installation time. Bitumen (Oil) pre-impregnated grids and composites requires approximately 25% less tack coat (oil) during installation between 0.10 to 0.15 gallon per square yard.
The gallon per square yard for Geocomposites is determined by the fabric weight. A 4.1-ounce ASTM 288-217 paving fabric will use a 0.22 - 0.25 gallon per square yard. The variance is determined if the application is on a new fresh oiled leveling course or an old asphalt. Installation considerations for a GeoComposite are different than if installing a paving fabric alone.
Grids that have adhesive or are bitumen impregnated may stick together creating tension when unwinding especially the rolls on the bottom of piles or van that have been compressed.
Regarding Paving Grids and Geocomposites, ask the questions. specification, equality, increased or decreased tack coat, type of tack coat (oil), roll widths, size and material of the roll’s interior cores. All will influence on your production time, costs and ultimately bottom line. Knowing the answers will help you make a correct decision on the selection and planning your installation.
Hybrid GeoMats are a nonwoven combination of polymers using fiberglass and polyester or polypropylene in combination to form a material with less elongation and a higher modulus. They function as moisture barrier & reflective crack prevention for alligator and medium cracks.
They install more rigidly then a geotextile and less rigidly then a geogrid. Each manufacturer has different recommendations and requirements for application, tack coat (oil) and for placement. There are no standard ASTM specifications for Hybrids.
They can be harder to place then both a geotextile paving fabric and a paving grid. Often their wrinkles can transverse the entire width of the material. The same procedures apply to placing a Hybrid Mat as with a Paving Fabric. Depending on the materials elongation they may install better with tensioning and some stretching or may install better with less impedance like a grid. They do not exhibit delamination problems and can handle traffic without damage.
Woven fabrics are higher-grab tensile strengths per ounce. They are thin and were found to be ineffective as a paving fabric since they have no interior plane to hold asphalt oil and therefore could not form an impermeable membrane. They also did not perform well as an asphalt reinforcement synthetic to reduce cracking or as a filtration fabric.
Woven fabrics have primarily two manufacturing processes and filaments. Woven slit films (tapes) are flat and have less filtration properties. They are best used in silt retention, separation and stabilization applications for their lower elongation and higher strength. Woven monofilament fabrics use round thick filaments and have apertures that permit for much better filtration and are best used in erosion control, slope protections or reinforcement where conductivity of water is desired.
Woven fabrics can be very beneficial in a rehabilitation project when a complete replacement of pavement is needed, and a new base installed prior to paving. They separate the base rock from the subgrade assuring a long term integrity and can add reinforcement stabilization by assisting in spreading the shear from local to general.
Nonwoven fabrics are primarily used in paving, filtration, drainage, separation and pond cushioning. The nonwoven fabric provides an interior plane (dimensional thickness) which allow for air passage in drainage (membrane cushioning), a better transfer of moisture in forming a filter cake in filtration and absorption of oil to saturate the fabric forming a membrane. Nonwoven fabrics can absorb up to 13 times their weight.
Nonwovens use thin filaments of polypropylene or polyester that can be needle-punched from short or long staple fibers or long continuous filaments.
Needle-punched (or entangled) fabrics are formed using two types of filaments. Barbed needles go up and down through the filaments entangling the strands together forming the fabric
Needle-punched fabric is thicker, fuzzy, softer and more pliable making them ideal for the paving application. They install smoother with fewer wrinkles due to their high elongation (stretch). Numerous reports state the fuzzy side placed into the asphalt oil provides reinforcement at the interface. The fuzzy side provides a greater effective surface area of the fabric offering better adhesive and shear strength with less slippage.
Nonwoven fabrics can be manufactured by one of three different processes for paving fabric which have a standard specification and installation procedures under AASHTO 288-17.
The most significant in the specification is 4.1 ounces per square yard and ultimate elongation greater than 50%. Not all agencies or engineers use AASHTO M288-17. Some have their own specifications and several states use 4.6 ounce. This will affect the tack coat application. A 4.1-ounce AASHTO M288-217 paving fabric will use a 0.22 - 0.25 gallon per square yard. The variance is determined if the application is on a new fresh oiled leveling course or an old asphalt. A heavier fabric will require more tack coat.
Individual nonwoven fabric specifications may appear to be nearly identical, yet the different manufacturing processes perform very differently during installation. AASHTO M288-17 uses MARV or minimum average roll value specifications. Many agencies require minimum test results may not accept manufacturer MARV certification and the fabric may pass MARV but fail testing on minimum
Of the three types of manufacturing processes listed below only number 1 has the qualities that are desirable for a paving fabric both for performance and installation.
A heat bonding (calendaring) is a finish that is applied to finish nonwoven needle punched fabric at the end of the manufacturing process. This can be applied to one or both sides of the fabric. This has special benefits to a paving fabric.
One sided heat bonded and one side fuzzy is the most beneficial and desirable paving fabric. It has numerous benefits:
The only installation problem that can occur is that the heat bonded on one side fabric can be placed upside down with the heat-bonded side down and the fuzzy side up. This presents the same delamination problems as non-heat bonded fabrics and additionally can cause fabric slippage from construction vehicles and if traffic drives on it. The heat-bonded side must be placed up to the traffic. The fuzzy side must be placed down to the old pavement.
Often manufacturers roll their material for machine placement, so the fabric comes off the roll and goes underneath the roll rather than coming off the top and this places the heat bonded side up and fuzzy side down. The roll must be loaded correctly onto the machine.
A non-calendared nonwoven needle-punched fabric is primarily for other than paving applications (filtration, separation, drainage liner cushioning). It creates paving construction problems with no tough wearing side. It almost always delaminates from any vehicle contact and even from oil oily foot traffic. FHWA-Texas report 261-2 mentions delimitation as a major problem with non-heat-bonded fabrics delaminating and fuzzing up in the wheel paths of traffic during construction. These problems create increased labor and slow construction. The damaged membrane in the wheel paths reduces long term performance. For this reason, it is best to use a calendared fabric with a tough wearing course for foot and vehicle traffic.
Dual sided calendaring creates a thinner, stiffer fabric. It is much harder to install and is more likely to have slippage, its wrinkles can be large and transverse the full width of the fabric. Its thinness has significant tack coat (oil) bleed through problems. These problems create increased labor and slow construction.
Paving fabric comes in a standard width of 12.5 feet but other sizes from 3 feet to 18 feet wide depending on the manufacturer are available or can be specially made upon request. Check what sizes your distributor stocks.
Both hot tack coat (oil) and rapid set emulsions can be used. Rapid set emulsions slow construction and must break completely before fabric is placed.
Hot bitumen tack coat is generally the preferred oil to use. The fabric can be placed into the oil almost immediately. One consideration is fabric shrinkage and melting. The oil is hotter then where fabric begins to shrink and melt. In the mornings and late evenings when the asphalt temperature is cool the oil cools rapidly and little delay is needed between spreading of the oil and fabric placement. In the day time when the sun has heated the asphalt to as much as 200 degrees the oil cools much slower and a delay between oil spreading and fabric placement may be needed to prevent shrinkage and melting of the fabric. Asphalt temperature is usually not a problem since the fabric is oil saturated and insulated from the higher temperature.
Overlaps and slit wrinkles require a double application of oil or the two thicknesses will not have enough oil to saturate both to form the membrane and bond the asphalt.
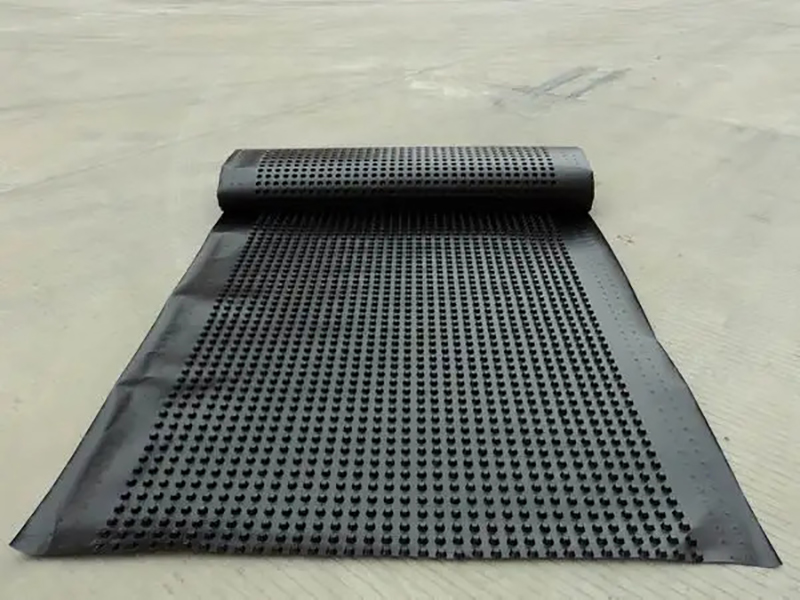
Geotextile Mounque “Monk” Barazone is owner of Geotextile Apparatus Company, manufacturer of the GAC Roller Puller and the Grizzly 600T and Grizzly Cub 300T geosynthetic installation machines. A presenter at the 2019 National Pavement Expo and a recent inductee into the Pavement Hall of Fame, he can be reached at [email protected] . The 52-page handout from his NPE 2019 presentation is available at www.gacco.com.