When choosing what sensor to use in different applications, it is important to first look at how they operate. Capacitive sensors generate an electrical field that can detect various liquids or other materials, such as glass, wood, paper, ceramic, and more at a close. Photoelectric sensors emit a light beam that is either received by a light sensor or bounced back to the emitter to detect an object’s presence or measure the distance to an object. Ultrasonic sensors bounce a sound wave off objects to detect them, which can make them a good solution for a surprising variety of uses.
Ultrasonic sensors operate by emitting an ultra-high frequency sound wave that ranges from 300 MHz to 3 GHz, which is well above the 15-17 kHz range that humans can hear that bounces off the target object. The sensor measures the amount of time that sound wave takes to return to calculate the distance to the object. Ultrasonic sensors send these sound waves in a wider beam than a photoelectric uses, so they can more easily detect objects in a dusty or dirty environment. And with a greater sensing distance than capacitive sensors, they can be installed at a safe distance and still function effectively Flow Meter 2 Inch

These capabilities together make ultrasonic sensors a great choice for tasks like detecting fill level, stack height and object presence. Sound waves are unaffected by the color, transparency, or consistency of an object or liquid, which makes it an obvious contender in the packaging, food, and beverage industry and many other industries with similar manufacturing processes.
So, to monitor glass bottles as they travel on a conveyor, an ultrasonic sensor could be a good choice. These sensors will consistently work well detecting clear or reflective materials such as water, paint, glass, etc., which can cause difficulties for photoelectric sensors. Another benefit of these sensors is the ability to mount them further away from their targets. For example, there are ultrasonics that can be mounted between 20 to 8000 mm away from the object. After tuning your setup, you can detect very small objects as easily as larger, more visible items.
Another common application for ultrasonic sensors is monitoring boxes. Properly implemented ultrasonic sensors can detect different sizes of boxes as they travel on a conveyor belt by constantly emitting and receiving sound waves. This means that each box or object will be measured by the sound wave. Different photoelectric and capacitive sensors may fail to detect the full presence of an object and may only be able to detect a specific point on an object.
When it comes to all types of different fill-level applications, there are many ways a sensor can monitor various liquids and solids. The width of an ultrasonic beam can be increased to detect a wider area of solid material in a hopper or decreased to give a precise measurement on liquid levels. This ability to detect a smaller or larger surface area gives the user more utility when deciding how to meet the requirements of an application. Although capacitive sensors can detect fill levels very precisely as well, factors like beam width and sensing distance might make ultrasonic a better choice.
With so many different sensor technologies available and factors like target material and sensing distance being such important factors, choosing the best sensor for an application can be demanding. A trusted expert who is familiar with these different technologies and the factors related to your applications and materials can help you confidently move toward the smart factory of the future.
Copyright ©2024. All Rights Reserved BNP Media.
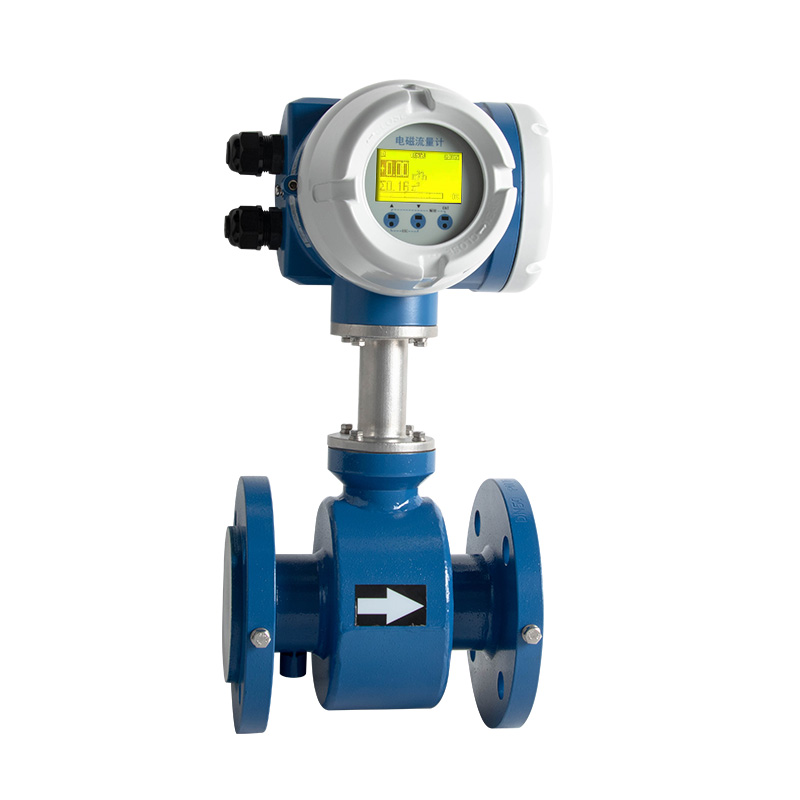
Pressure Transmitter Design, CMS, Hosting & Web Development :: ePublishing