We use cookies to enhance your experience. By continuing to browse this site you agree to our use of cookies. More info.
Ferrous materials contain iron, either as the primary element or in combination with other elements. These materials are widely used in construction, automobile, aerospace, and many other industries because of their strength, durability and versatility. Auto Components
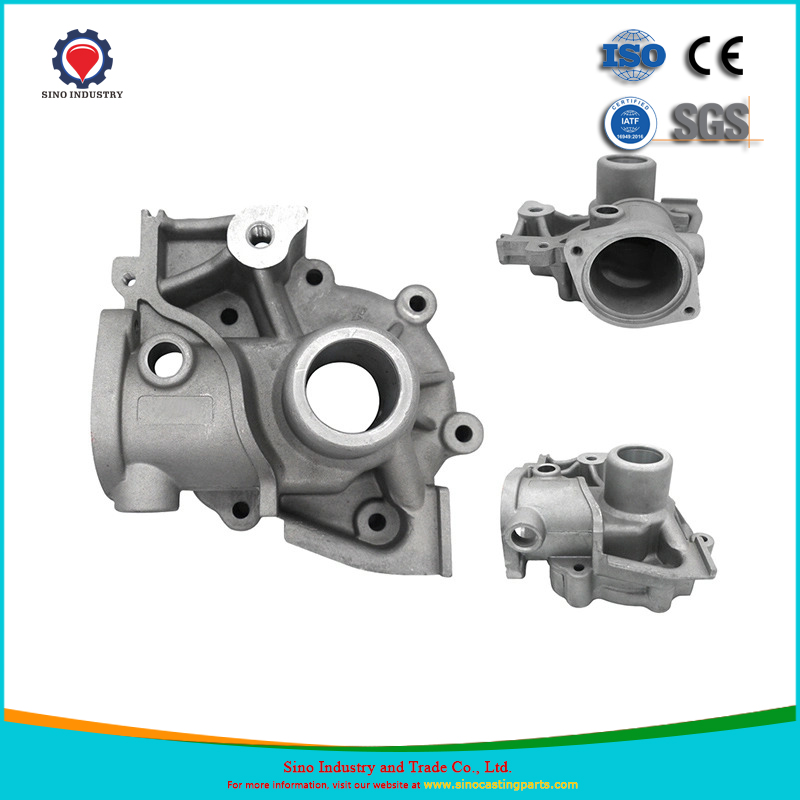
Image Credit: luca pbl/Shutterstock.com
Ferrous materials can be classified into two main categories: pure iron and iron alloys. Pure iron, also known as wrought iron, is a relatively soft and ductile material that contains less than 0.1% carbon. It is not commonly used in modern applications because of its low strength, but it was widely used in the past for making tools and artifacts.
Iron alloys, on the other hand, are much more commonly used in modern applications. These alloys combine iron with one or more elements, such as carbon, manganese, vanadium, molybdenum, cobalt, nickel, or chromium. Adding these elements can significantly improve the mechanical and chemical properties of the material.
Ferrous alloys have a wide range of properties that make them suitable for various applications. Here are some of the most common types of ferrous alloys and their applications:
Carbon steel is an alloy of iron and carbon, with carbon content typically ranging from 0.05% to 2.1%. It is widely used in construction, automotive, and machine-building due to its high strength and low cost.
Stainless steel is an alloy of iron, chromium, and sometimes nickel, with at least 10.5% chromium content. It is known for its high corrosion resistance and is widely used in the food processing, medical, and aerospace industries.
Alloy steel is an umbrella term for a wide range of ferrous alloys that contain other elements such as manganese, chromium, nickel, and molybdenum. These alloys are designed to provide specific properties, such as high strength, wear resistance, and corrosion resistance, and are used in various applications, such as automotive and aerospace.
Cast iron is an alloy of iron, carbon, and silicon, with carbon content typically ranging from 2.1% to 4%. It is known for its high hardness and excellent castability and is used in applications such as pipes, engine blocks, and cookware.
Wrought iron is an iron alloy with a very low carbon content, typically less than 0.1%. It is known for its high ductility and is used in fencing, gates, and ornamental ironwork applications.
Steel is a crucial material in most vehicles and is expected to maintain its dominance in the future because of its exceptional mechanical properties. Advanced high-strength steel meets the essential criteria, including strength, high fatigue life, formability, crashworthiness and cost-worthiness. One of the recent developments includes steel foams for the automobile bumper to absorb the crash energy, hence saving the chassis or frame from deformation.
Maraging steel, with a strength of up to 2200 MPa, is widely used in manufacturing high-performance aircraft components, rocket motors, missile systems, and other aerospace and defense applications. The class of ultra-high-strength steel (UHSS) is a critical component of the aerospace sector; with 7% of the aircraft weight, the turbine bearings and the landing gears are preferably made with this material.
Ballistic steel is a type of steel specially designed to protect against various kinds of ballistic threats, such as bullets and explosive fragments. It is also known as armor steel or bullet-resistant steel. Ballistic steel is made by alloying various metals, such as nickel, chromium, and molybdenum, to create a material that is extremely hard and strong. The Vickers hardness number of these materials ranges between 500-590 VHN combined with strength up to 1900 MPa.
Mild steel has reasonably good strength and has a thermal expansion coefficient (9 x 10-6 /˚C) similar to that of concrete (8 x 10-6 /˚C) and hence is a key component for application in modern-day skyscrapers and mega structures.
Complex space frames widely used in railway bridges and structures are popularly made of high-strength steel with exceptional fatigue properties. Some examples include the Chenab rail bridge, operational at 1178 ft. and the Eiffel tower, completed in 1889 AD and still standing tall at 1083 ft.
An essential process in achieving the high strength of the steel is the heating and cooling process designed to attain specific microstructures within the material. These microstructures are specific arrangements of atoms to provide high resistance to deformation. The various documented microstructure of steel includes martensite in the Widmanstätten structure, pearlite, bainite, ferrite, austenite and cementite. The coexistence of the microstructures with fine grain structure enhances the strength and is widely used.
The most effective means of enhancing the service strength and getting desired properties such as corrosion resistance and high fatigue life is alloy addition. The systematic inclusion of one or more materials in small quantities to achieve desired properties different from the parent material is called alloying. For example, adding chromium to steel results in stainless steel, which is highly resistant to corrosion and can be used in applications where the steel will be exposed to moisture or corrosive substances.
Other elements that can be added to steel include cobalt, nickel, vanadium, tungsten, and titanium, improving strength and toughness. By carefully selecting the elements to add and controlling the amount of each element, it is possible to tailor the properties of the resulting steel to meet specific application requirements.
There are several limitations regarding microstructure refinement through heat treatment alone. Thermomechanical processing involves mechanical deformation during heat treatment.
Ultra-high-strength steel is a result of alloying in addition to thermomechanical processing.
Ferrous alloys have several advantages that make them widely used in various industries. However, there are also several disadvantages associated with their use. For example, ferrous alloys can be susceptible to corrosion, weakening the material and reducing its useful life. This is particularly true for alloys exposed to harsh environments or corrosive substances.
Ferrous alloys tend to be heavy, which can be a disadvantage in specific applications where weight is a concern. For example, reducing weight is a crucial design goal in the automotive and aerospace industries, and non-ferrous alloys such as aluminum and titanium are often used instead.
In addition, the production of ferrous alloys can have a significant environmental impact due to the energy and resources required to extract and process iron and other metals. In addition, using certain alloying elements, such as chromium, can create toxic waste products that must be carefully managed and disposed of.
Additive steel manufacturing involves using various techniques to create a part, layer by layer, using a powdered form of desired steel and a laser or electron beam as a heat source to selectively melt and fuse the powder. The additive manufacturing of steel offers several advantages over traditional manufacturing techniques, such as creating complex geometries, customized parts, and reducing material waste. It also enables the production of parts with improved mechanical properties, such as strength and toughness, due to the fine control over the microstructure that can be achieved during the process.
J. N. Hall, et al. (2017). Steels for auto bodies in Automotive Steels. Elsevier. doi.org/10.1016/B978-0-08-100638-2.00002-X.
J. Li, et al. (2023). Progress on improving strength-toughness of ultra-high strength martensitic steels for aerospace applications: a review. Journal of Materials Research and Technology, doi.org/10.1016/j.jmrt.2022.12.177.
A. Heidarpour, et al. (2014). Mechanical properties of very high strength steel at elevated temperatures. Fire Saf J, doi.org/10.1016/j.firesaf.2014.01.006.
Y. Tomita. (1991). Development of fracture toughness of ultrahigh strength low alloy steels for aircraft and aerospace applications. Materials Science and Technology. doi.org/10.1179/mst.1991.7.6.481.
P. K. Jena, et al. (2010). Effect of heat treatment on mechanical and ballistic properties of a high strength armour steel, Int J Impact Eng. doi.org/10.1016/j.ijimpeng.2009.09.003.
G. Thewlis, et al. (2004). Classification and quantification of microstructures in steels. Materials Science and Technology. doi.org/10.1179/026708304225010325.
Disclaimer: The views expressed here are those of the author expressed in their private capacity and do not necessarily represent the views of AZoM.com Limited T/A AZoNetwork the owner and operator of this website. This disclaimer forms part of the Terms and conditions of use of this website.
Akanksha is a Ph.D. research scholar at the Indian Institute of Technology, Roorkee, India. Her research area broadly includes Graphene synthesis by the chemical vapor deposition technique. Akanksha also likes to write science articles regarding the latest research in 2D materials, especially Graphene, and reads relevant papers to understand what is being claimed and try to present it in a simplified way. Her goal is to help every reader understand Graphene Technology, regardless of whether their background is scientific or non-scientific. She believes that everyone can learn - provided it's taught well.
Please use one of the following formats to cite this article in your essay, paper or report:
Akanksha, Akanksha. (2023, April 07). A Guide to Ferrous Materials. AZoNano. Retrieved on September 20, 2023 from https://www.azonano.com/article.aspx?ArticleID=6409.
Akanksha, Akanksha."A Guide to Ferrous Materials".AZoNano.20 September 2023.
Akanksha, Akanksha. "A Guide to Ferrous Materials". AZoNano. https://www.azonano.com/article.aspx?ArticleID=6409. (accessed September 20, 2023).
Akanksha, Akanksha. 2023. A Guide to Ferrous Materials. AZoNano, viewed 20 September 2023, https://www.azonano.com/article.aspx?ArticleID=6409.
Do you have a review, update or anything you would like to add to this article?
We take a closer look at the fusion of nanotechnology and CAR-T therapy through our interview with Dr. Roey Elnathan about a new approach that harnesses the capabilities of nanoneedles to efficiently deliver genetic materials to target cells.
In this interview, Laura-Isabelle, the Director of Sales at Photon etc., talks to AzoNano about how spectral imaging can help improve the next generation of solar cells.
In this interview, we speak with Sixonia Tech about the company's highlight product, E-Graphene, as well as their thoughts on the future of Europe's graphene industry.
The Verifire™ interferometer system provides fast and reliable measurements of surface form error.
Discover the compact, fast rotary table V-610 for precision testing and manufacture.
The Diamond Interaction Chamber (DIXC) is integral to the NanoGenizer high-pressure homogenizer.
AZoNano.com - An AZoNetwork Site
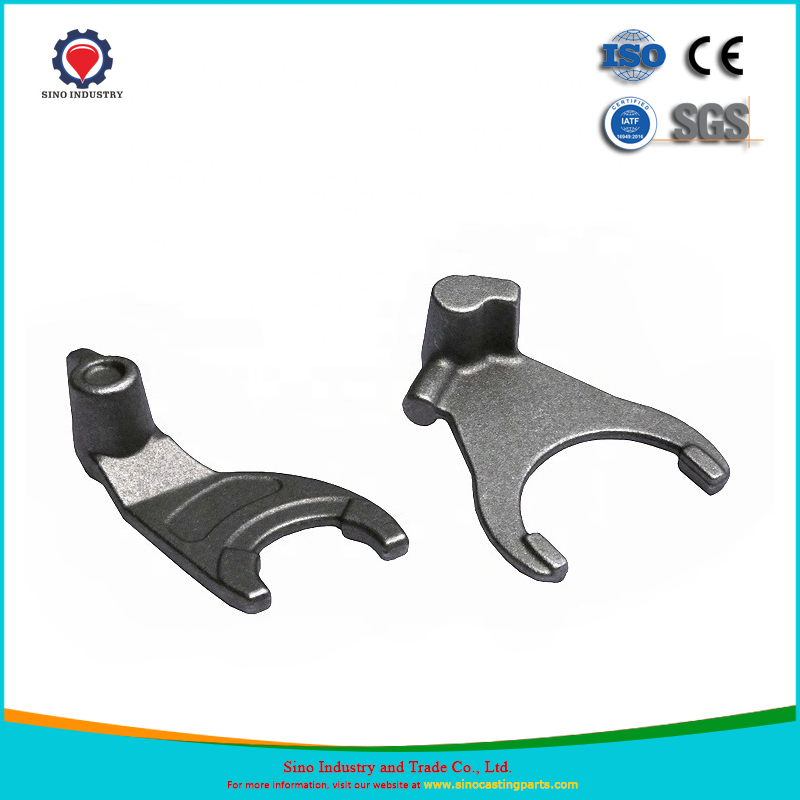
Metal Accessory Owned and operated by AZoNetwork, © 2000-2023