Driven, a new company spun out of CeramicSpeed, has shown its innovative Orbit Drive transmission for the first time at Eurobike, Frankfurt. The working prototype of this all-in-one gearbox eBike motor weighs a claimed 4.6 kg – including all gears, electronics, and power delivery to the rear wheel – and can be configured to produce up to 90 Nm torque.
The design takes inspiration from systems found inside hybrid cars – like the Toyota Prius, for example. Therein, planetary gears are utilized to mesh the input of the combustion engine with the input of an electric motor, to deliver power to the vehicle. Right Angle Bevel Gearbox

Driven are taking that concept and, instead of using flat, planetary gearing, their Orbit Drive relies upon a rotating ball-like mechanism that delivers a variable speed ‘bevel differential’. Though the layout is certainly not novel, its application in eBike technology, is.
We are told by Driven, “This is a game changer for the e-bike segment, bringing the highest level of efficiency (more battery range), a more pleasant riding experience, almost zero-maintenance, and a bolt-on solution for e-bike manufacturers”.
Here, Driven’s Head of Engineering, Ryan Norris, takes the time to explain the mechanism using a neat 3D printed model of the concept. And, he does so in terms that don’t require a PhD in mechanical engineering in order to comprehend.
The Driven Orbit Drive is a little further along in its development process than the above 3D printed model might suggest. The company has a working prototype they say is significantly more efficient in its energy usage than any production eBike motor on the market today – upward of 85%, is the claim.
Not only that, but maintenance intervals are set to once every 10,000 miles, with only an oil change required at that point. Clearly, such a design boasts some serious advantages over commonly available eBikes that rely upon a motor and an entirely separate derailleur-operated drivetrain – the pitfalls of which many of us know all too well.
Driven tell us their system also offers a smoother ride experience, with an automatic mode offering step-less shifting with gearing automatically adjusting speed, with the assist motor complementing the rider’s input. Manual mode is also possible, allowing riders to shift through gears as they would on what Driven are calling a “legacy bike”, i.e. a regular bike.
In addition to the claimed higher efficiency over comparable systems, we are told the Orbit Drive also has a regenerative braking feature to compound that.
Driven plans to offer three variations on the Orbit Drive to its OEM customers:
We asked Brian Baker, CEO of Driven, why has no one done this yet. His answer…
“One of our marketing pitches is – why hasn’t anyone done this? I’ve been the CEO for one year, and I do not have an answer for that. Everyone took what they are doing at Toyota, on the Prius, and at Stellantis for example – those are all flat planets and sun gears. All we did was take the planet and do that [make it that 3D orbit shape]. Now, it fits right in the middle of a q-factor, and we can get a 1:1 ratio out of the motor. We don’t have to downshift the motor, so we can use smaller motors, and so this whole thing works quite a bit better than a flat, planetary system”.
Driven has more technology packed into there, too. Unlike most eBike motors on the market today, this one lacks a torque sensor, at least in the traditional sense. Driven hold a key patent for a sensor-less torque sensor.
“There’s an algorithm we’ve developed based on how much torque you’re putting into the system – and thus how much torque the motor sees – from that you can calculate the speed, so you don’t even need sensors at all“.
“We’re using the electronics of each motor, and how they talk to each other. So, when they sense you pressing down on the pedal – they know it within about 40 ms, and we’re gonna get that down to about 20 ms, so that’s as fast as a regular torque sensor is. So, we don’t need the torque sensor. And torque sensors are actually pretty expensive, so we’re actually pretty excited that this algorithm works. It’s nothing new. It is used in industrial mechanical design all the time but no one has ever used this in the bike industry before”.
We are told that, in terms of the Ride Share market, the Orbit Drive will come in at a middling price point – more than the $800 USD that the cheapest offerings go for, but less than the $1,500 USD that higher-end options go for.
Brian goes on to tell us he is confident that gearbox eBike motors of this design, and similar, will become the most common design in the market over the next 10 years.
Indeed, with the launch of Pinion’s Mission ON:E eDrive earlier this week, the industry certainly seems to be pressing on with integrated solutions to shifting and assistance. Likely, we will see many more such offerings on display in the vast halls of Messe Frankfurt this week.
Jessie-May Morgan is the UK & Ireland Tech Editor of Bikerumor. She has been writing about Mountain Bike Riding and Racing, and all its weird and wonderful technology for 4 years. Prior to that, she was an Intern at the Mountain Bike Center of Scotland, and a Mountain Bike Coach and Leader in the Tweed Valley.
Based in Innerleithen, Scotland, Jessie-May can often be seen riding the Glentress Trail Center, and its neighboring Enduro and Downhill Tracks. She regularly competes in Enduro at a national level, and has recently competed on the World Stage at a handful of Enduro World Series events.
For Bikerumor, Jessie-May is testing the latest mountain bikes, equipment and kit, letting readers know what’s hot and what’s not.
For context, she weighs 60kg and stands at 5ft 4″ tall (163cm).
This site uses Akismet to reduce spam. Learn how your comment data is processed.
Jessie-May Morgan has written many a fine technical article. This one is in a different category.
The device described in this article seems entirely different from the device shown in the pictures and on the manufacturer’s Web site.
“…a rotating ball-like mechanism that delivers a variable speed ‘bevel differential’…” I thought this meant that, in principle, it operates like a Kopp Variator or its copy, the Nuvinci. They transmit power though friction between a set of hard balls and two round plates they run against, the input and the output. Adjusting the angle of the balls achieves the variation in speed. These devices require a thixotropic fluid to manipulate the friction.
Further study, however, indicates that the author means a simple differential gear, ancient in principle, that one can imagine as a rotating ball. But there are no hard balls in this device, no friction, no special fluid and no explanation of how the variable speed is obtained (see below). It is nothing whatsoever like a Kopp.
Describing any part of this mechanism as a planetary gearbox reveals a misunderstanding of the planetary principle. There is no planetary action in this device. Please disregard any such statements.
“… This differential allows for two inputs (a rider and electric power), to combine into one output that drives the back wheel…” [manufacturer’s statement on the Web site].
In other words, it obtains variable speed in the same way that a super-imposing gearbox does, with two independent inputs that determine the output. This is an excellent method. The article does not mention it.
“…available eBikes that rely upon a motor and an entirely separate derailleur-operated drivetrain – the pitfalls of which many of us know all too well…” This is a low blow.
Chain drive with derailleur(s) is the dominant technology for several excellent reasons. It is the most efficient, it is simple, it weights the least and it costs the least. It works fine with a minimum of attention. Since it is dominant, parts are easily found throughout the world.
And it is easy to install a motor on it.
No doubt the Driven Orbit Drive works as advertised. I do not believe it will sell. It is easier to obtain the same results with a simpler and cheaper and lighter and more efficient arrangement, especially one that does not require a special bike frame. That is, there are many ways to install such a system on a standard bike without requiring any modification of the frame.
To be fair, this is not an easy article to whip up without a pretty extensive understanding of the mechanics behind it.
The “ball-like” description is not ideal when you know how a Nuvinci CVT works, but few people know that. I got a copy of the Orbit Drive press release today and it uses the term “ball-like” several times (I assume as a result of the 3D printed bevel “ball” shown at 2:20 in the video), so you cannot blame Jesse-May for that.
And planetary gears are described on the differential Wikipedia page, notably under “ring and pinion designs”: https://en.wikipedia.org/wiki/Differential_(mechanical_device)
Contrary to what I wrote below, a differential is a planetary device. I stand by the rest of it.
Bevel gears have inherently higher losses that straight gears. Engineering textbooks say that there is at least a 5% loss for every 90º change in the direction of torque. Count them.
So, this is a 3 motor system. One is the rider legs, connected to the satellite carrier. The second is connected to right bevel gear = output The third is connecter do left bevel gear. By electronicaly controlling the speed ratio between the electric motors you change the mechanical ratio from the legs to the output.
Think that sum think about when they hitt up Shimano derailleurs cassette mechanical parts that’s moving bike notice different between freely moving, n moving slow fighting against pase they set for adjusted to can scale normal pace get caught up traffic speed steady even pace constantly felt as norm high also forced back on safety prior concern
As explained, it works similarly to the Toyota e-CVT. This, when applied to e-bikes, is similar as well to the E2Drives system announced for Decathlon’s bike (there are some other patent applications for e-bikes from different companies).
The working principle is a compound hybrid system using a “power-split” setup. The power split is a 3-axle gear (two inputs and one output or vice-versa) and can be performed using a planetary gear, a differential, or others. Functioning principle: * The first axle is the BB spindle as the human power input. * The second axle is connected to the first motor/generator which adds SPEED to the third one, and it is linked in torque with the 1st one; therefore, there is no need for a torque sensor (the electrical intensity t its stator is proportional to the pedaling torque). * The third axle is connected to the output and, in parallel, to a second motor/generator which adds TORQUE.
Managing the electric power from one motor to the other you choose from high torque (low speed) to high speed (low torque) which indeed acts like a shifting mechanism.
All I had to read was that Ceramicspeed was behind it and I knew it would be full of gimmicks. Take a lofty goal, inject some VC investment, and you get things that make headlines, but don’t make it to market.
Shaft drive was one of the earliest drivetrains applied to bicycles(nearly all other drive systems have been applied decades ago as well), but it has naturally fallen out of favor due to its inherent inflexibility in fitment. It’s lossy, heavy, and requires a special frame. No bueno on all counts. The weight can be reduced, slightly, but the other issues are inherent to the design. No amount of whizbang carbon ceramic pvd cryo-treatment can solve those.
Chains win the efficiency game every single time.
Interesting but looks heavy. The driveshaft has its own issues. Watching to see where this goes.
The RSD Wildcat V3 will help you keep the Rubber Side Down even if you tackle bigger trails.
Pivot’s mid-wheeled enduro mountain bike starts to grow up with a new 29er front end.
Because chances are your existing pumps are costing you watts with their piddly little gauges.
Can we say N+1! State Bicycle Co. is ready for winter snowfalls with all-new affordable alloy 6061 Trail+ Fat Bike that won’t break the bank…
Zwift will let you save about $30 by switching to an annual plan, but you’ve gotta pay in full up front. And what’s up with their trainer?
Insta360 Ace Pro delivers AI-powered creative effects, a huge sensor, and gesture control!
All-new sleek Rotwild R.R275 X gravel ebike combines futuristic angular looks with neat TQ & lighting integration, plus custom controls…
Buy the aluminum & carbon Frameworks DH Bike Frame now, the US-made development project of pro downhiller Neko Mulally…
Sign up to receive BikeRumor content direct to your inbox.
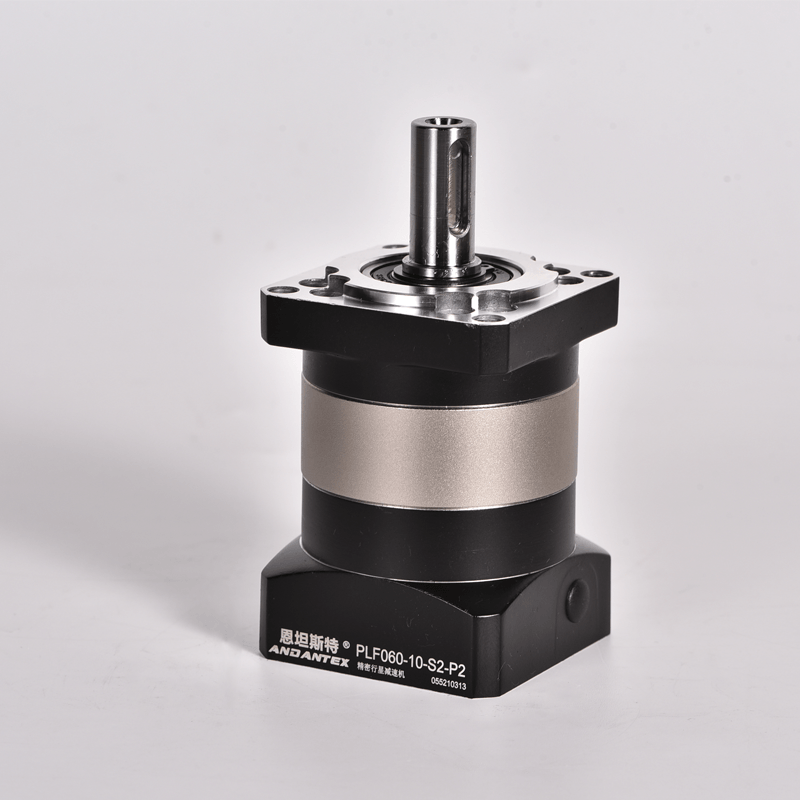
Safeguard Gearbox Sign up to receive BikeRumor content direct to your inbox.